SimLex Scheduler Function
SimLex Scheduler can be linked with host system SimLex ERP or SimLex Production Control. SimLex Scheduler is automatic scheduler and after scheduling, you can edit schedule result easily by manual.
The operation procedure is to create scheduler data by MRP of the host system → execute automatic schedule → manually edit the schedule result → import the schedule result in the host system → issue production order / subcontract order → create purchase order by MRP of the host system → issue purchase order.
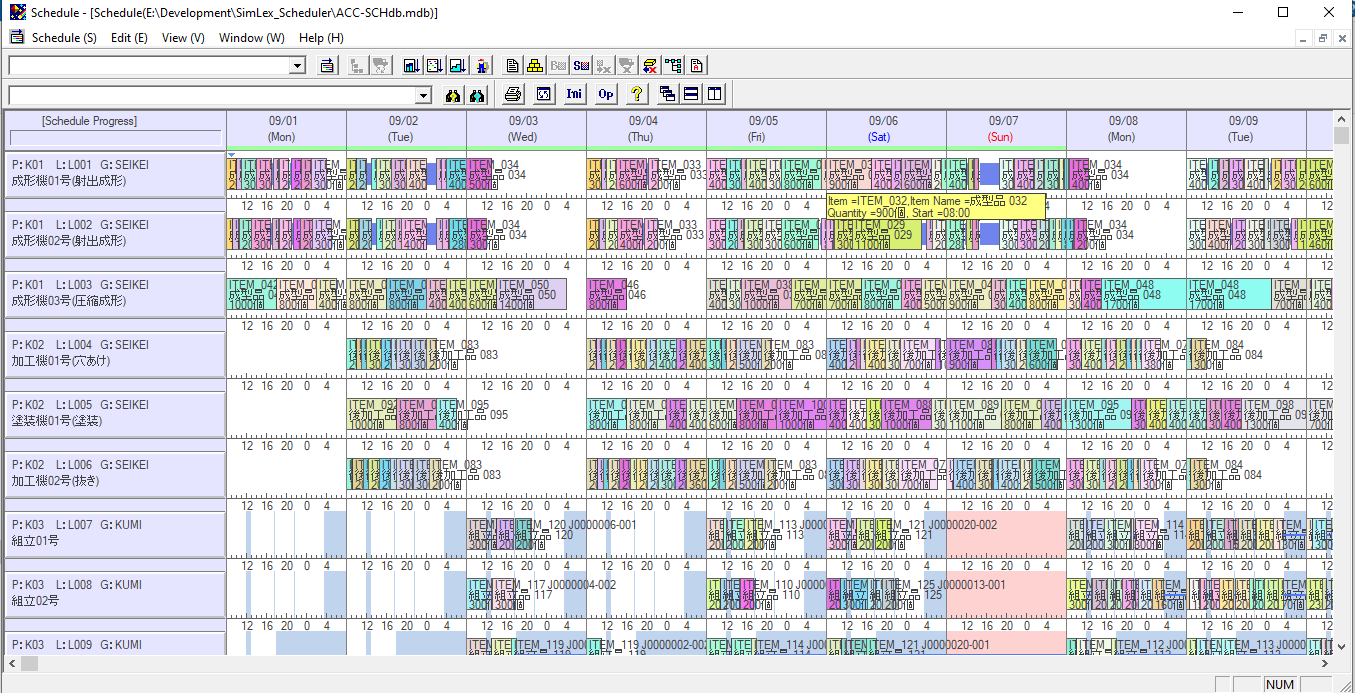
Various Scheduler Gantt Chart
Equipment Gantt Chart
Worker Graph
Lot Gantt Chart
Process Stock Graph
Item Gantt Chart
Equipment Load Graph
Scheduler Optimization
[Delivery Optimization]
Scheduling is done with priority given to the delivery date. If the delivery date is the same, scheduling is performed in order of order with the earliest delivery time.
[Set Up Optimization]
As long as the delivery date allows, we can optimize the setup time to the minimum and the maximum operating rate. For the setup time, fixed setup such as cleaning and variable setup depending on the item produced before that are available. It can be optimized for each equipment in a multi-stage process.
[Quality Optimization]
As long as the delivery time allows, we can optimize the order of color, temperature, material, etc. for the best quality. Same as with the optimization of setup, it is possible to optimize for each equipment in a multi-stage process.
[In-Factory / Subcontract automatic distribution]
If the load of the in-factory production is excessive, it will be automatically distributed to subcontract. At this time, consider the difference in lead time between in-factory production and subcontract.
[Equipment Connection Function]
In a multi-stage process, it is used when intermediate work-in-process produced at a specific equipment in the upstream process must be produced at a specific equipment in the downstream process.
[Optimizing Days] (Enable Forward / Backward Scheduling by Item)
You can set the production date ahead of schedule for each multi-stage process. This allows you to set 'Operating rate production', 'Synchronized production', 'Semi-operating rate production, Semi-synchronized production' for each item. It is possible to consider the strategy of the production method for each item.
[Same Time Production]
Scheduling is possible when two or more items can be produced at the same time with the same equipment in the press process, injection molding process, and machining center process.
[Worker Optimization]
When considering worker restrictions, schedule within restrictions such as the number of worker in the production worker group and the decrease in production capacity due to the reduction in worker. If you do not consider worker constraints, calculate the number of worker required.
[Automatic Over Time]
In the process of daily scheduling, if scheduling will delay in delivery unless production or setup change is performed outside the standard operating hours of the day, scheduler will make a plan in consideration of overtime and holiday work according to the operating mode.
[Considering Purchase Receive]
You can schedule the delivery plan of the purchased item as a constraint. If there are no restrictions, the required quantity of purchased items will be calculated.
[Considering Set Up Jig]
You can register molds as jigs and schedule within the limit of the number of jigs. You can also consider the repair period and the number of repairs for the jig.
[Considering Max Stock]
Schedule so that the maximum stock is not exceeded because there is no place to store stock or you do not want to increase in-process stock. The maximum stock can be set for each process / item.
[Considering Safety Stock]
In safety stock, scheduling is executed to secure a certain amount of stock.
[Over Lap Function]
The production of the post-process can be started after a certain period of time from the start of production of the pre-process. This function makes it possible to shorten the manufacturing lead time.
[Load Ratio / Average Load Ratio of Replacement Equipment]
In the load allocation of alternative equipment, when a specific item can be produced by multiple equipment, the load is allocated to the equipment with free load according to the priority. At this time, the maximum number of alternative equipment is 99. In the average load allocation, scheduling is performed so that all line loads in the same process are averaged.
[Storage Function]
Scheduling that considers tanks in a continuous process system is possible. Efficiently schedule shared tanks, taking into account tank stock.
[Use-Up Function]
In a batch process, the surplus stock can be used up for the specified items.
[Full Pegging Function]
When you click the production instruction on the Gantt chart, real-time pegging is performed not only for the lot product but also for the MRP controlled product, and the linking information is displayed from the finished product to the input process. Pegging information can be output to the database.